ABB Railway Technologies To Tackle The Steepest Challenge On The Pilatus Railway
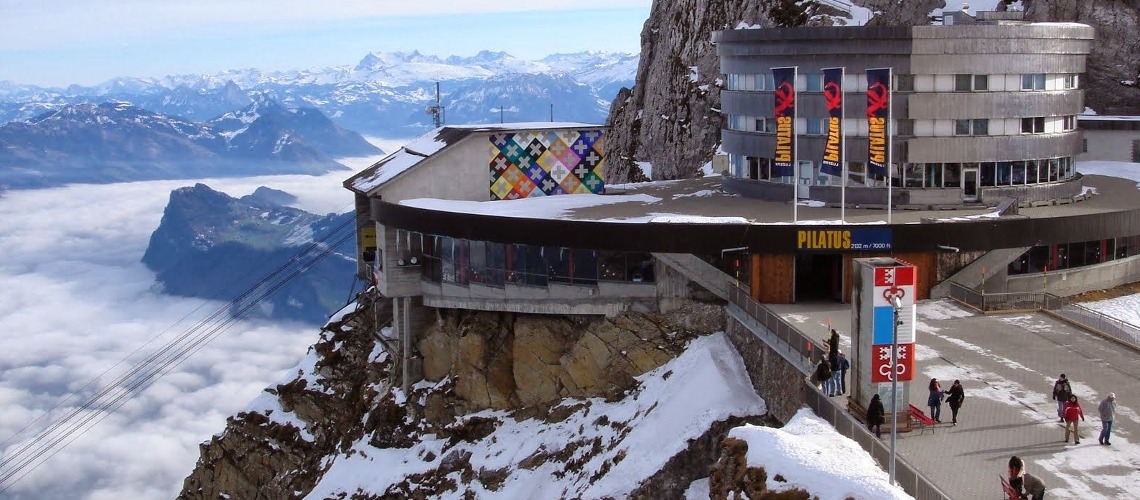
Pilatus Bahnen, operator of the world's steepest cogwheel railway, which has a maximum gradient of 48 percent, has put a new, more energy-efficient fleet of eight railcars and one freight car into operation on the popular Swiss excursion mountain. Built by leading train manufacturer Stadler, the new rack rail cars feature energy-efficient ABB traction technology that contributes to more efficient, reliable and sustainable rail operations.
"We are pleased to put this new generation of cogwheel trains into operation, which are equipped with ABB traction converters with the latest drive technology," says Godi Koch, CEO of Pilatus-Bahnen AG. "These enable more energy-efficient operation and increase the comfort and speed of the journey for our guests."
Gil Fischer, Local Division Manager ABB Traction Switzerland says: “We are very pleased that drive solutions from ABB are also being used in the latest generation of vehicles and that we are supporting Pilatus Bahnen on the way to continued reliable and even more efficient rail operations.”
The planning, construction and test phases extended over a period of several years in close cooperation between ABB and Stadler, as the project was extremely demanding. The design of the new trains calls for the largest possible glass fronts and a panoramic glass roof to improve the view for visitors to the Pilatus. In addition, the narrow gauge of the Pilatus Bahn and the horizontal pinion limit the available space for electrical components. Therefore, ABB was asked to develop a new, powerful, but compact, light and robust solution to be placed under the wagons.
Thanks to ABB's energy-efficient traction converters, the new cog railcars also consume 30 percent less energy than the previous generation. When braking, the electrical energy generated is fed back into the grid and is available for the ascent. This works in such a way that the motors, acting as generators, convert the kinetic energy into electricity, which flows back into the overhead line via traction converters, instead of converting the braking energy into waste heat.
By converting the braking energy into electrical energy, also for the emergency power supply of the vehicle, the descent is guaranteed even if the supply from the overhead line is interrupted.
The tailor-made ABB traction converter solution is compactly housed in a single housing. Two traction converters are installed underfloor in each train unit. They convert the electrical energy from the overhead line into the voltage and frequency required to drive the traction motors.
Pilatus is a popular destination for hundreds of thousands of Swiss and international guests. The 4.6 kilometer route between Alpnachstad and the Pilatus Kulm terminus reaches an altitude of 2073 meters above sea level and offers a wide view of Central Switzerland. The cog railway climbs over 1,600 meters in altitude with an average incline of 35 percent and a maximum incline of 48 percent.
ABB offers a wide range of innovative and tailor-made drive solutions for the diverse requirements of the various rail vehicle concepts. ABB technologies tailored to customer needs are also used reliably, for example, on the meter gauge and rack railways of the Appenzell Railways, the Bernese Oberland Railway, the Matterhorn Gotthard Railway, the Rhaetian Railway and the Central Railway.
ABB is a leading technology company in electrification and automation, enabling a more sustainable and resource-efficient future. The company's solutions combine technical expertise with software to improve the way things are made, moved, powered and operated. Building on more than 130 years of excellence, ABB's approximately 105,000 employees strive to drive innovation to accelerate industry transformation. www.abb.com