Steamboat Snowmaking Future-Proofed With TRM Cast Iron Pipes
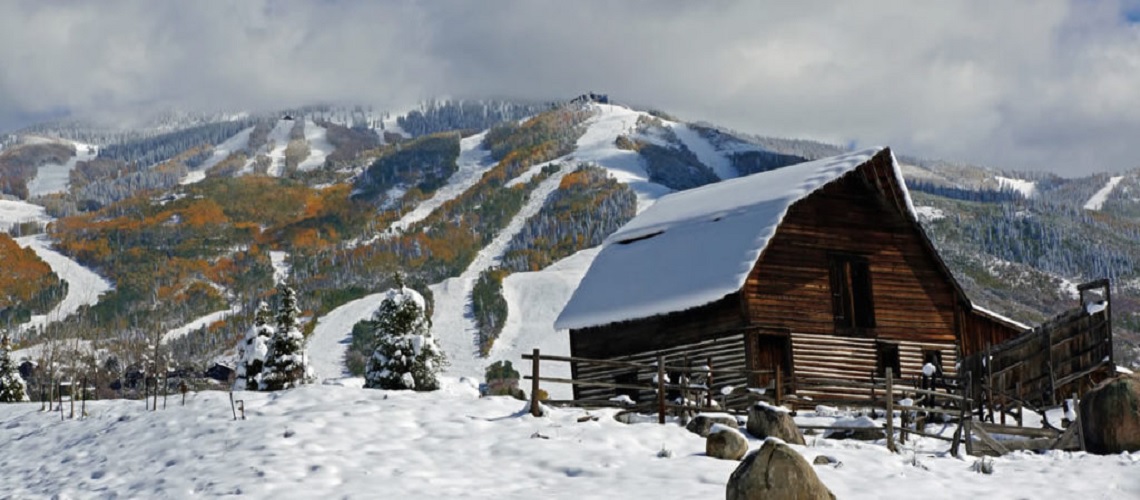
In the early 2000s, the Steamboat Ski Resort experienced leakage problems from the steel piping of the snowmaking system installed in 1981. In addition, the pipes led through areas with complex supply systems in lower-lying regions. In 2006, Steamboat Ski Resort decided to replace all of the steel tubing on this runway.
A new piping system had to be found that could handle the high pressure demands in all pipe sizes, ensure better longevity and reduce costly repairs in the future. In addition, it must be possible to install it quickly and easily, especially on the steeper terrain of this slope. In addition, the new piping system must be flexible to accommodate the limitations in low-lying areas imposed by larger utility systems. Ultimately, environmental damage should also be minimized in the entire project region.
Steamboat management began product research to review and evaluate other piping systems that could improve the performance of the steel system. As part of this research, Steamboat contacted PNP Supply engineers for more information on TRM's VRS®-T system. Based on this product research, Steamboat selected TRM's ductile iron piping system for a number of reasons.
A key criterion when installing piping in any alpine region is the selection and use of materials that protect ecosystems and best preserve the integrity and sustainability of natural resources.
- Ductile iron pipes from Tiroler Rohre GmbH (TRM) offer unique properties such as e.g.:
- Ductile iron pipes are made from over 98% recyclable materials.
- The execution of the connections does not require welding or open flames at any time during assembly/installation.
- The assembly of the connections takes place with considerably little effort.
The ease of assembly and the smaller/lighter construction equipment means that installation can be carried out in a much smaller footprint. This reduces the effort for post-processing and clean-up work.
Assembly/installation can be completed in a very short time.
In the course of the project, a total of 5.41 km of high and low pressure lines with diameters of DN80 to DN300 and a pressure of up to 100 bar were laid. Between 2011 and 2022, 27.5 km of high-pressure pipe were installed. In addition to the top product quality, the focus was on the very good customer service, the best possible delivery reliability/availability and the extensive product range. The more than 30 years of experience of the Tyrolean family company TRM as a pioneer in the snowmaking industry rounded off the picture.