Fatzer: Faster Delivery Thanks To Lean Management
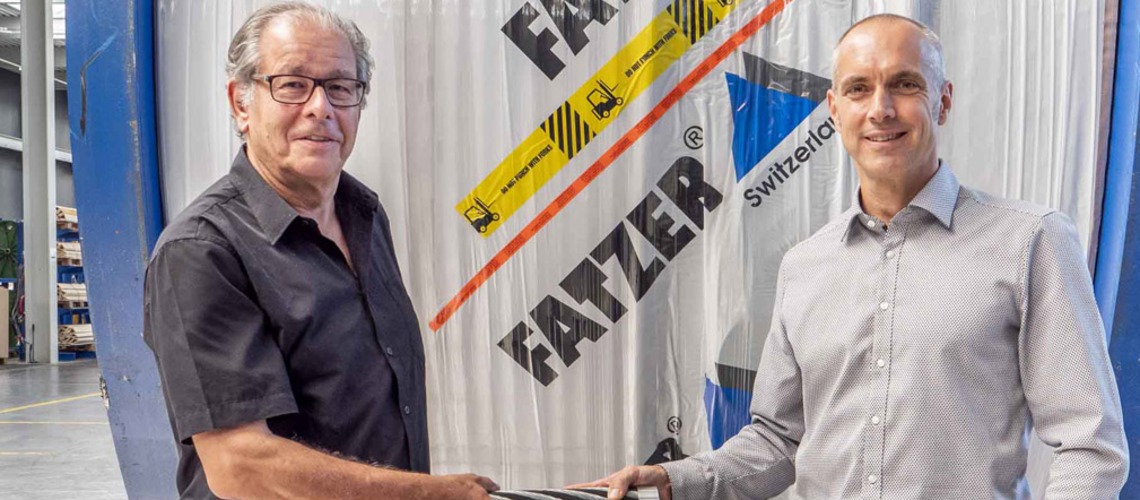
In recent years, FATZER has implemented continuous improvement (Kaizen, Japanese "way of improvement") and radical change (Kaikaku, Japanese "reform") into the workflow through numerous audits. The involvement of employees in the optimization of processes is essential because they are the most important component for the successful implementation of lean projects. The employees were therefore encouraged and motivated to face the changes not with resentment but with an open mind instead.
How the customers benefit from lean management
Satisfied customers are FATZER's top priority. Thanks to the consistent streamlining and optimization of processes, it is now possible to realize inquiries in a very short period of time, especially in case of an emergency.
When the stranded rope of the "Sea to Sky Gondola" in Squamish, Canada, was severed in an act of vandalism on August 10th, it initially looked like a season involving heavy losses for the operator. Many employees were worried about the future of their jobs.
Earlier than planned
However, when FATZER assured the operator a new production and express delivery of the 4.5-kilometer long stranded rope with a weight of around 55 tons, fortunately, the tide turned.
Soon after, the success story began to take its course. Only 3 days after the accident had happened, the steel wire was ordered and exactly one month later, the production started. Thanks to the perfectly timed logistics, the finished rope was loaded onto the truck more or less directly from the stranding machine and, after a journey of 8,275 kilometres, it was unloaded in Squamish exactly one month later.
Thanks to perfectly coordinated production processes, a smooth flow of goods and the highly motivated FATZER team, the order was completed earlier than planned.